PROPERTY DEVELOPMENT PROJECT HIGHLIGHTS
PROJECT 1: Decontamination and Demolition Management of a Petroleum Technology Center

Landmark’s precedent-setting Materials Management Plans for the closure of an 80-acre Petroleum Research facility was recognized by the U.S. Environmental Protection Agency for Significant Achievement.
During this six-year facility deactivation and decommissioning project, Landmark conducted environmental due diligence, developed project specifications for decommissioning, and provided industrial hygiene and abatement management services for building demolition and contaminated soils remediation to support the closure of an 80-acre former Petroleum Technology Center in Colorado. We evaluated and performed a cost-benefit analysis for the waste management and recycling processes and supported the implementation of waste consolidation.
Our client received the U.S. Environmental Protection Agency Environmental Excellence Award for Voluntary and Significant Cleanup. The Asbestos in Soils Program Landmark developed for the site was later incorporated into newly promulgated Solid Waste Regulations in the Colorado Revised Statutes.
PROJECT 2: Demolition Management of a Major Manufacturing Site

Landmark safely completed a seven-year decommissioning and demolition of a major aerospace manufacturing site during the transfer of the property from Brownfield to Greenfield Redevelopment.
Landmark successfully designed and managed the environmental decontamination and demolition of the one-million-square-foot industrial building on the 45-acre former Hamilton Sundstrand Denver Metal Works facility. The facility included multiple buildings that began operations in the 1950s, was decommissioned in 2003 and 2004, and demolished in 2007 and 2008. Corrective action plan investigations continued at this site until 2019.
Manufacturing processes in this facility included machining, welding, electroplating, painting, heat-treating, nondestructive testing, and waste treatment. Landmark identified and managed contaminated soils and successfully developed the first Soil Characterization Management Plan in Colorado managed under dual regulatory jurisdictions. Our programs for the site were submitted during the promulgation of new applicable regulations, and our plans were accepted by the regulators with only minor comments.
Landmark provided turnkey services during the decommissioning phase and performed extensive industrial hygiene monitoring throughout the project for asbestos, metals, polychlorinated biphenyl (PCBs), and other chemicals during the demolition phase. Landmark and our affiliated toxicologists performed a Human Health Risk Assessment for PCBs. Our staff also conducted hazardous waste evaluations and identified proper treatment and disposal methods.
The property was developed in consortium with former owners, Brownfield and Greenfield developers, municipalities, and state health regulators. This project was completed on time and within budget contingencies.
PROJECT 3: Demolition Management of a Major Retail Redevelopment Project
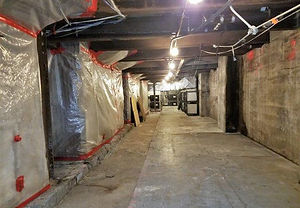
Redevelopment of a 100-acre major commercial property required conscientious environmental technical services to support reliance by numerous lenders.
The redevelopment of a Colorado commercial and major retail site was initiated with the closure of the site, followed by environmental abatement and structural demolition of the 900,000-square foot facility. Landmark performed planning and environmental permitting, including federal, state, and local permits for the National Pollutant Discharge Elimination System, National Emission Standards for Hazardous Air Pollutants, and Clean Air Act. Asbestos inspections were conducted, and abatement oversight was performed, resulting in no violations or safety incidents.
The abatement work was valued at more than $1.5 million, and Landmark’s data quality resulted in less than 5% in change orders during demolition. Close coordination of environmental abatement and demolition activities resulted in an aggressive six-month schedule for site closure, which was attained. Landmark conducted inspections and Environmental, Health, and Safety Reviews of the abatement, which was performed closely with site redevelopment activities in a high traffic/active construction area. We successfully negotiated regulatory approvals of the management of non-friable asbestos during demolition, resulting in lower costs and increased re-use and recycling of building materials.
PROJECT 4: Environmental Remediation of an Historical Munitions Arsenal
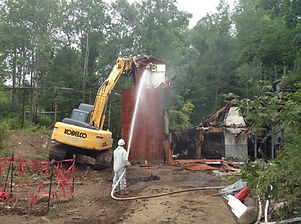
Industrial Hygiene Assessments were conducted in close concert with Explosives Safety Surveys in 82 Buildings at a 200-year-old Arsenal.
Picatinny Arsenal is the oldest continually operating arsenal in the United States and specializes in advanced conventional weapon systems and advanced ammunition life cycle management, research, development, and acquisition. As a team member for the Facilities Reduction Program, Landmark conducted Asbestos, Lead, Polychlorinated Biphenyl, and Other Regulated Material (ORM) Surveys at 82 structures operated since the Korean War. The ORM assessment included assessments and inventory of hundreds of locations with stored chemicals and chemicals/oils in process systems, lighting wastes, and refrigerants.
Because this project included numerous areas with hidden materials and unforeseen conditions, Landmark’s robust project controls and quality assurance focused on safety and addressed specific investigation-related, data-gap concerns that were proactively identified by our experienced personnel. These project controls were adopted by other team members. A key success of this project was our ability to anticipate hidden materials and address them through destructive sampling and other means.
Following the completion of the Site Characterization Surveys, Landmark developed facility abatement and hazardous materials removal cost estimates and work plans for these large and complex abatement projects. Landmark performed oversight and industrial hygiene monitoring and successfully confirmed compliance during decommissioning and demolition of these structures, including several explosively-contaminated buildings.
PROJECT 5: Industrial Hygiene Monitoring to Support Elevator Rehabilitation at Carlsbad Caverns National Park

The design of environmental controls and air monitoring program protected the public and environment at this United Nations Educational, Scientific and Cultural Organization World Heritage Site.
Carlsbad Caverns National Park provides visitors access to some of the largest limestone caves in North America. To access the caves, elevators were constructed in 1932 and 1954 to transport guests and cargo to the caves approximately 750-feet below. Water seepage, humidity, and time contributed to the corrosion of the structural steel components in the elevator shaft. This project included complete replacement of structural steel components during a structural demolition and rehabilitation project within the elevator shaft.
Landmark provided air monitoring during media abrasive blasting, rock removal with pneumatic equipment, grinding of steel surfaces and lead abatement activities, and application of industrial coatings. The objective of the air monitoring was to prevent exposure of the public and the environment to harmful levels of dust, volatile organics, and lead particulate, as well as evaluation and protection of natural resource conservation concerns such as noise and temperature/relative humidity levels in the caves. Monitoring was conducted in the occupied portions of the Visitor Center and sensitive cave areas adjacent to the elevator shaft to protect the public, staff, and certain threatened/endangered species within the cave.
Landmark’s industrial hygienists also conducted Quality Assurance Inspections and oversight to ensure that project complied with project design specifications and applicable regulations. Ongoing projects include Radon Exposure Assessments and ventilation/engineering evaluations for worker and visitor safety.